フェルトができるまで
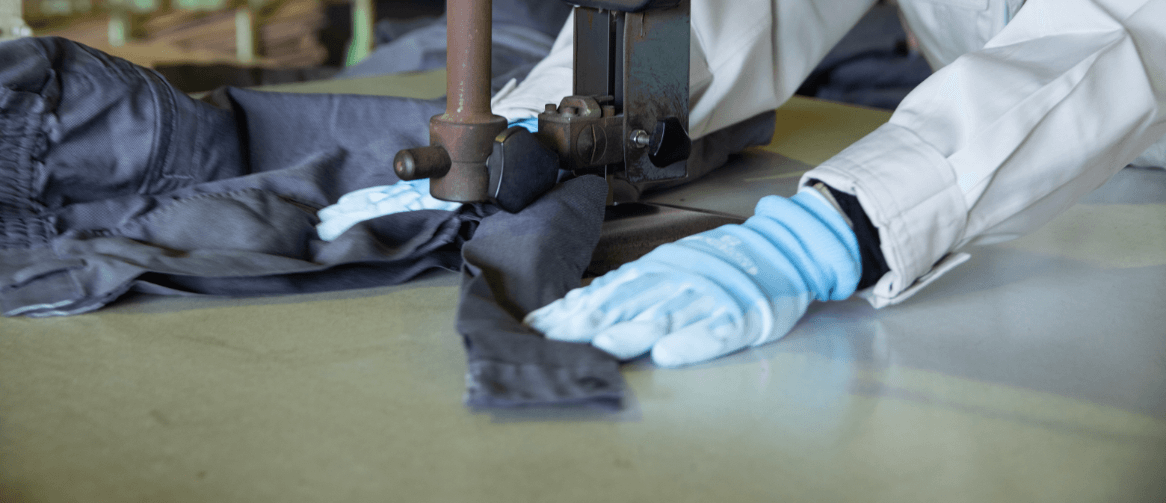
反毛生産工程(エー・ケー・テック)
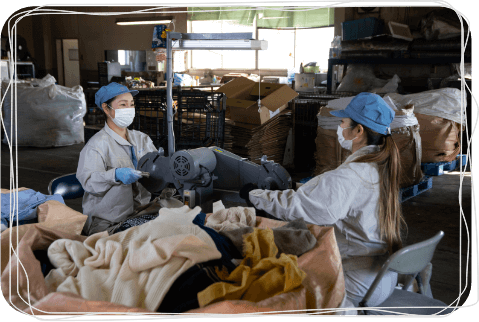
01 選別
フェルトの原料となる「反毛」は、全国から集められた古着・ユニフォーム・繊維くず等をリサイクルしています。
集まった古着を組成(綿・化繊など)で選別します。
その後、金具やファスナー、ボタン等は手作業で丁寧に除去したものが反毛の原料となります。
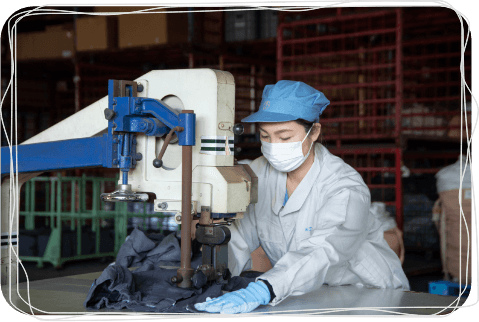
02 裁断
原料を裁断機で適当なサイズに裁断します。
ギロチン刃や、ロータリーカッターでこまかく裁断していきます。
裁断工程では原料の配合も行うため、生産する反毛に基づいた分量をそれぞれ裁断機に投入します。
※配合パターンに合わせ、どの素材を何キロ投入するか、計算しながら作業を行っています。
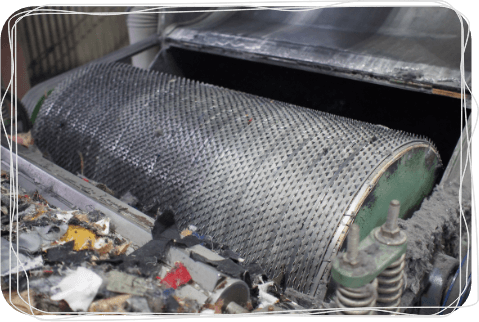
03 開繊
細かく裁断された原料は、ダクトを通って混綿室へと運ばれます。
積層された原料を混ぜ合わせて混綿が完成します。混綿を反毛機で開繊し、反毛を完成させます。
開繊機の刃(シリンダー)は消耗すると火災の原因になるため、こまめに交換&チェックを行います。
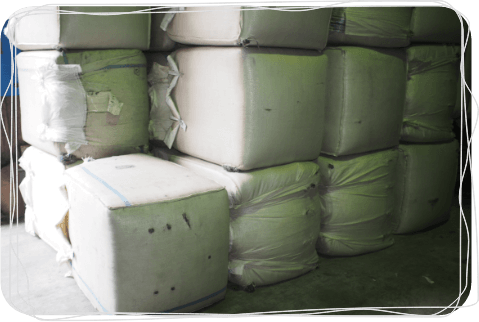
04 梱包
「ドンタ袋」と呼ばれる袋に反毛を圧縮梱包し、「反毛」の生産が完了します。
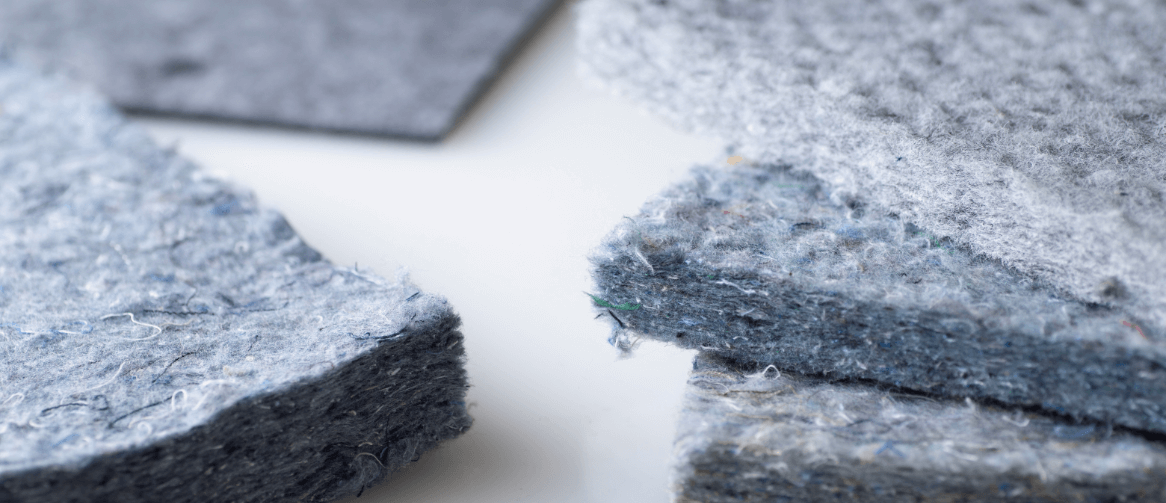
フェルトの生産工程
-
01 原料投入と混綿
原料ホッパーに原料を投入し、原料を撹拌します。ギザギザの刃がついたシリンダーを使い、繊維をほぐして混ぜ合わせていきます。
-
02 フリース製造
混ぜた原料を平らにし、「フリース」と呼ばれる状態に成形します。フリースをムラなく均一な厚みにしていきます。
-
03 熱処理
平らにしたフリースは、まだふわふわの状態です。フリースに硬さを持たせるために、熱を通す処理を行います。繊維に熱を入れて冷ますと固くなり、フェルトになっていきます。
-
04 厚み調整
最後のmmの単位の細やかな調整を行います。
-
05 裁断
幅には「スリッター」、縦には「シャーリング」と呼ばれる刃を用いて裁断を行います。
-
06 金属探知機
完成したフェルトに金属が混入していないかをチェックします。
-
01 原料投入とレジンの混ぜ合わせ
原料ホッパーに原料を投入し、フェノールレジンを入れ、原料と混ぜていきます。
製品に合わせて投入量を調整しています。 -
02 フリース製造
混ぜた原料を平らにし、「フリース」と呼ばれる状態に成形します。フリースをムラなく均一な厚みにしていきます。
-
03 熱処理
原料を鉄板に挟み、熱を加えていきます。
※ここで半分ほど熱が入った状態のものを「セミフェルト」と呼びます。セミフェルトは完成したレジンフェルトに比べて加工しやすいため、別の製品工程へと運ばれます。 -
04 裁断
幅には「スリッター」、縦には「シャーリング」と呼ばれる刃を用いて裁断を行います。
-
05 金属探知機
完成したフェルトに金属が混入していないかをチェックします。
-
01 原料投入と混綿
原料ホッパーに原料を投入し、原料を撹拌します。ギザギザの刃がついたシリンダーを使い、繊維をほぐして混ぜ合わせていきます。
製品合わせて細かく計量をし、原料を配合していきます。 -
02 ウェブ製造工程
「カード機」と呼ばれる機械を使用して、原料を薄いシート状にし、何層にも重ねていきます。シート状に重なったものを「ウェブ」と呼びます。
-
03 ニードルパンチ機
ニードルパンチ機を用いて重ねた原料を上下から針を刺して繊維を絡めていきます。繊維の結合が強まり、何層ものシートが接着され、1枚のフェルトになります。
-
04 裁断・巻取り
スリッターと呼ばれる刃を用いて、幅方向の裁断を行い、巻き取っていきます。
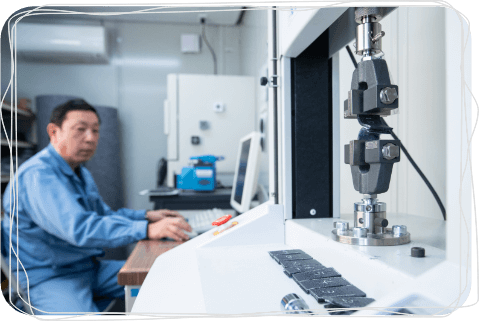
検品・出荷
フェルトにはさまざまな出荷状態がありますが、旭タカロンではすべての工程に品質チェックの担当者がいます。 厚みや不良品のチェックを行い、基準を満たしたフェルトだけをお客さまのもとにお届けしています。
旭タカロンのフェルト加工技術
製品貼り合わせ加工
針を用いて部品やフェルト同士を接着させる「タッカー」、樹脂を用いた「ホットメルト」など、用途に合わせた製品の貼り合わせを行います。ゴムとフェルトの接着には環境にやさしい水溶性接着剤を使用します。
ニードルフェルトの熱処理加工
2〜3層のニードルフェルトを熱処理で貼り合わせる加工です。ポリエチレンフィルムをニードルフェルトの間に挟み、熱で溶かして表層と下層を接着させます。
断裁加工
お客さまのご要望や用途に合わせ、サイズを適時調整します。
スライス加工
厚みのあるフェルトを用途に合わせ、薄くスライスします。
ホコリ・毛羽立ち防止加工
フェルト表面に毛羽たち防止剤を塗布して乾燥させ、埃・毛羽立ちを防止します。